Greater Washington builders explain pros, cons in wood, steel or concrete frames, featuring J. Reid Glennie
When planning a new building, whatever that building’s ultimate purpose, there’s one decision that must be made early on — what material to use for the structure itself.
There are generally three options: wood, steel and concrete. We wanted to know what the experts thought about each one, and just how they pick each building’s frame material.
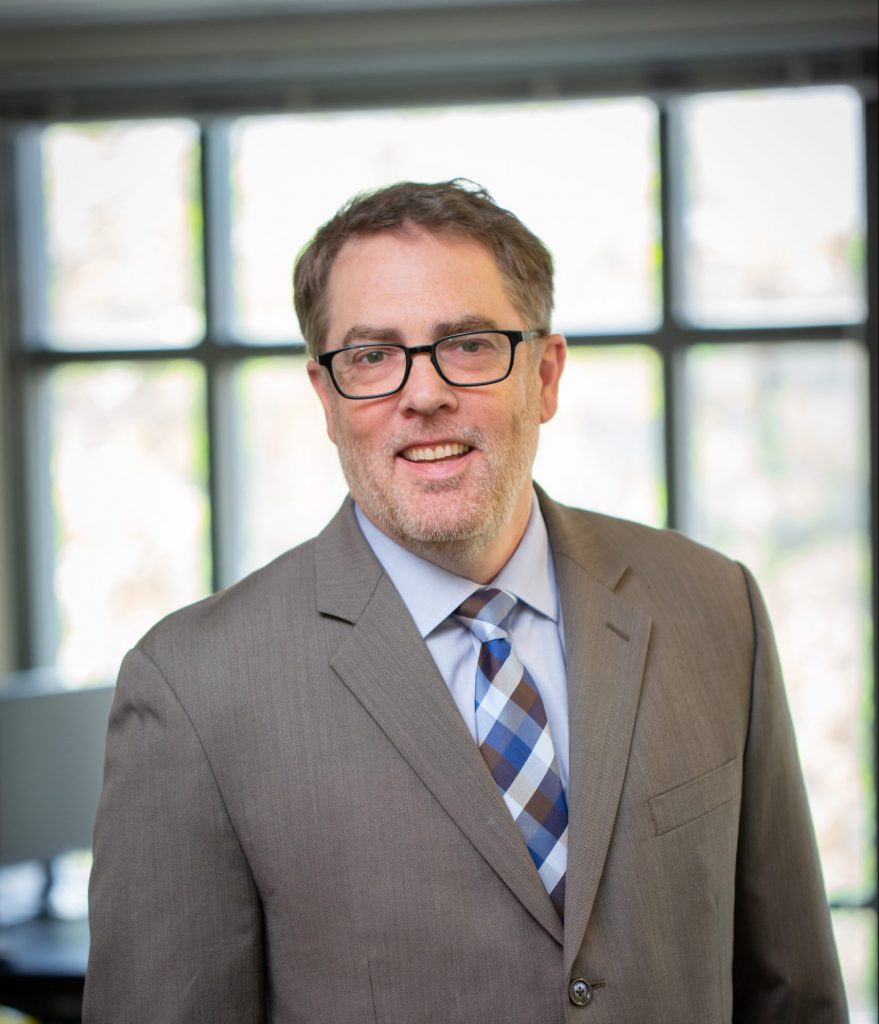
The experts:
- Steve Burke, director of sustainability, Consigli Construction Co. Inc.
- Joel Causey, project executive, construction, Redbrick LMD LLC
- J. Reid Glennie, director of construction, Jair Lynch Real Estate Partners
- Patrick McCrary, partner and senior preconstruction manager, Coakley & Williams Construction
- Michael Pittsman, principal, James G. Davis Construction Corp.
- Nihar Shah, partner, Perseus TDC
- Seth Thompson, director of preconstruction, Holder Construction Group LLC
Wood
The pros: Perhaps the biggest thing wood has going for it is a lower price tag. It’s by far the least expensive of the three and also requires less labor than some, involving only one trade. It’s also lightweight, quick to build with and, some would say, the most adaptable. Wood is also better for insulation, and its use could reduce energy costs in the long run. The only exception to its lower price is mass timber, which Joel Causey of Redbrick LMD said is much closer in price to steel or concrete.
In addition to these practical considerations, wood is also the most environmentally friendly material. In expanding more on this, Steve Burke of Consigli Construction said, “The use of wood, and specifically mass timber, can have a considerable advantage when it comes to achieving environmental goals when the wood is harvested and utilized sustainably. Inevitably, materials sourced from our built environment like steel and concrete generate greenhouse gas emissions while they are produced, whereas the use of wood stores carbon even after the trees have been cut down. Additionally, by utilizing wood, we are able to leverage existing, naturally occurring materials in a project’s design and construction.”
The cons: It has limited applications due to fire code — you can’t use it as a building frame for something bigger than five stories. Extra precautions must be taken to protect it from fire or mold. And there’s still a chance it can warp, shrink or swell from exposure to the elements.
The best uses: Patrick McCrary of Coakley & Williams Construction and J. Reid Glennie of Jair Lynch Real Estate both said wood is perfect for low- to mid-rise multifamily, ideally a wood frame on a concrete podium. Seth Thompson of Holder Construction Co. also said it works well for some lower-end retail buildings, while Michael Pittsman of James G. Davis Construction said that firm is starting to use mass timber for more high-rise office buildings. And as Burke emphasized, wood is often the best choice if sustainability is your top concern.
Anyone’s favorite? Thompson of Holder and McCrary of Coakley & Williams both picked wood as their least favorite to work with. “It is very simple and repetitive, less complex and elegant,” Thompson said. But for Consigli’s Burke, “when sustainability is a priority, along with the specific aesthetics of a project, we have found that mass timber is often selected by the project team,” noting that Consigli has especially made use of wood lately for higher education projects.
Redbrick’s Causey was even more emphatic. “Hands down, we would choose mass timber,” he said, adding that this type of wood has a better resistance to fire than other kinds. “Mass timber can be used to create a variety of architectural designs, from simple structures to complex buildings. It can be left exposed, creating a natural and warm aesthetic, or it can be concealed behind other materials.”
Steel
The pros: Speed is a big advantage to using steel. Nihar Shah of Perseus TDC estimated it can reduce your construction schedule and personnel by 15%. This is because so much of it will be prefabricated and manufactured to your specifications off site. It’s also very strong and durable, to the point where it can even be reused if a building is demolished. It’s highly weather-resistant and requires little upkeep. And due to how it’s assembled, steel framing can also allow for more open floor layouts with fewer columns, allowing for peak flexibility.
The cons: Steel production is very energy-intensive and costly. And while you can build very quickly once you have it, it can take a while to get it delivered, especially if there’s, say, a supply chain issue — a challenge seen often during the pandemic. And while it’s not actually flammable itself, steel conducts and transmits heat from a fire more than any of these other materials. For this reason, it has no natural fire rating. McCrary said using sprayed-on fireproofing and a concrete deck are recommended. Also, as Thompson pointed out, while it can offer great flexibility in the design phase, once you have your steel in hand, you can’t change it — so it has the least amount of flexibility on site. “Steel buildings can have a negative impact on the environment in several ways,” Causey said. “The production of steel involves the extraction and processing of iron ore, which requires a significant amount of energy and can result in carbon emissions, as well as other environmental pollutants, such as sulfur dioxide and nitrogen oxides.”
The best uses: Steel is the frame of choice for high-rises, agreed Shah of Perseus and Glennie of Jair Lynch Real Estate — think 20 stories or more. McCrary prefers steel for mid-rise office, life science or education projects. Thompson also picks steel for warehouses and other industrial buildings.
Anyone’s favorite? Shah picked steel as his favorite, for all its strength and time-saving capabilities.
Concrete
The pros: Cast-in-place concrete is incredibly flexible as a building material, as it can be molded to virtually any shape you want, which “allow designs to incorporate interesting features and flexible spaces,” said Pittsman, of James G. Davis. With concrete, floor thickness can be thinner, thus maximizing that space, which comes in handy when you have a building height limit. It’s also strong, able to support the heaviest load, and dense enough for the best sound attenuation.
The cons: Concrete is also not particularly eco-friendly, generating carbon emissions. It’s also vulnerable to erosion and even mold, as it’s a porous material. There’s also the curing time required in its use, which can mean the longest construction time, said Causey. It can also require the most on-site labor to work with, including multiple trades and intensive quality control testing, said Glennie. All of these factors together contribute to raise the cost of using concrete.
The best uses: Due to its high fire resistance and structural durability, Causey picks concrete for hospitals, nursing homes or any place that might serve as a storm shelter. Pittsman and McCrary both like it for high-rise office and multifamily, especially in D.C., and also see precast concrete used a lot for data centers. Glennie and Shah both said it’s ideal for buildings higher than nine stories but fewer than 20.
Anyone’s favorite? Pittsman is a concrete guy. “The DMV is a cast-in-place kind of town,” he said, especially due to height restrictions. Plus, you can build any shape. Glennie likes it best due to its density and strength. Thompson agreed: “This is personal, but I think concrete, because as a builder, it is enjoyable to see all the raw ingredients of a building structure come together in front of your eyes through the hands of skilled tradesmen. It is more of an exhibition of the complexity of construction which is fascinating and intriguing as a builder,” he said.